Coming to Warley
Some time during the 1850s James Turner, son and grandson of wicker workers of Oakthorpe in Derbyshire, left his village and migrated south to Birmingham. In the 1851 census he is a 13-year-old basket maker, and by the next census (1861) he is married with a toddler and a baby. Mary Ann Morley would bear him fourteen children, six of whom would die in infancy. All surviving boys learnt their father's craft in Irving Street and Upper Gough Street, Birmingham.
From Nuneaton and its crowded Abbey Street, Joseph and Maria Johnson, together with their seven children, likewise migrated to Birmingham about 1866; two years later Maria was a widow - she was pregnant and had five children still at school. The two older boys were working in the brass industry but life must have been desperately hard for her. Nevertheless within a few years Johnson's Fruit Market in Sherborne Street was established and the business would remain for the best part of a hundred years. Her grandchildren have told me of the fun their mothers had being pushed in the cart as groceries were bought from the wholesale markets around Horsefair; I guess the return trip was less fun.
By the 1880s, after twenty years in the confines of old Ladywood, the Johnsons again got itchy feet. Charles Henry Johnson, the eldest son, had inherited property in Nuneaton and was a successful businessman. He was on the lookout for greater possibilities beyond the city boundaries. Already owning several houses in Ladywood, he managed to acquire a row of brickmakers' cottages in what is now Kenilworth Road off Birch Road, near to where the Wolverhampton Road meets Hagley Road West. It is tempting to say ‘just below the Warley Odeon’ but that would make little sense to anyone under 40…
It is unclear from the records who occupied the cottages when they were bought by Charles Johnson but the adjacent brickworks (Airey’s ‘brickle’) was either closed or about to close. Personal memories of Birch Road from the turn of the century by Daisy Bourne, a Johnson cousin, can be read in Rosser’s book [1].
On the 24th of October 1889 Maria Johnson, daughter of Joseph and Maria, married James Turner, eponymous son of our incomer from Oakthorpe, at Christ Church, New Street, Birmingham. The church is long gone, but was approximately where the 'floosy in the jacuzzi' now flaunts herself in Victoria Square and is remembered in the flight of steps between New Street and Waterloo Street. Family history insists that James senior was an organist at this church.
While Charles Henry Johnson was establishing the, now, quite numerous Johnson families in Birch Road, James and Maria were resident in Ladywood but very soon moved to Quinton, as it then was. |
|
|
|
|
Birch Road area in 1910 |
The Basket Business
Various trade directories suggest the basket business was not established until the early years of the 20th century, but evidence in the form of an old notebook provides an earlier date.
By this time basket making by the Turners, man and boy, had been established for 40 years in Birmingham and undoubtedly trusted contacts enabled the business in the new premises to start up quickly. The workshop was a curious building, the back half of a terrace of four back-to-back houses with no back houses. Access to the first floor where baskets were stored was via an external wooden staircase with the help of a rickety ladder - the top floor was very scary. |
|
|
|
|
Notebook entry from 1898 |
The workshop was on the ground floor. Through stable doors three or four workmen would be sitting on the floor, and inclining away from them would be a flat baseboard in the centre of which was a metal spike, perhaps 3 inches in length. The spike was shiny and polished through continual running contact with the willow as the basket was turned while the men threaded the softened willow through the uprights. In the air was the characteristic smell of the craft, a pleasant, earthy smell.
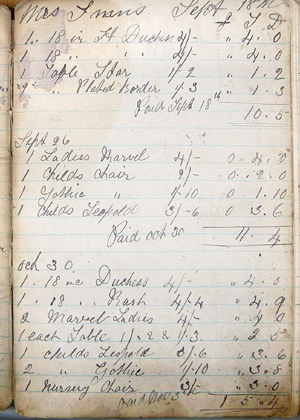 |
|
Returning to the Victorian notebook, we can see that while baskets of many sizes and designs were the bulk of the trade, ‘cane’ furniture was also of some importance. A child's chair at 2/-, a childs Leopold at 3/6 and a Ladies Marvel at 4/- are the prices in 1897.
The pay for a wicker worker in 1916 was 8d or 9d per hour for a 52½ hour week [2]. It is difficult to make sense of this unless we have some idea about one could buy with such seemingly petty sums: suffice to say you did not retire early on a basket maker’s pay!
Invalid chairs and spinal carriages were part of the output of the basket works especially during and after WWI, and hence the occupation of, surgical appliance maker was deemed ‘scheduled’, and James Turner continued making baskets throughout the Great War. This must have been at a much diminished output as journeymen basket makers were called up in the latter years of that terrible conflict. Sadly, James was a victim of the influenza pandemic and died in 1918.
Just before James passed away, his only son, the author’s grandfather, James Charles, always known as 'Charl', was called to service in France. His time with the colours was brief and he returned to re-establish the basket works where he worked until well beyond his eightieth year. |
Furniture sales |
|
My late father's younger brother writes [3]:
"The period I remember most clearly is from 1935 to 1950, when the backbone of the business was the brown boiled osier work sold in Birmingham Market, and have always understood that that had been the case from the start of the business.
Of course during both the First and Second World Wars there was a demand for spinal carriages and bath chairs made from buff willow which had been boiled and peeled creating a finer material, but as far as I am aware only Grandad, Uncle Arthur and Dad made these items:, the other men were still employed making the pots and hampers [4]. During WW2 the Ministry of Defence ordered a large number of 'Airborne Hampers' for dropping by parachute to supply forces on the ground. They were made of a white willow from Argentina with very long stems almost 20 foot (more than 6 m) supplied by the Ministry.
It was only in the declining years of the business, say from 1950 to 1970, that Dad turned over to buff and white [5] used in picnic hampers, cycle baskets etc.
|
|
|
|
|
'Charl' making picnic hampers |
Rabbit hampers were larger and more substantial than the fruit pots with a very heavy border approx. 2ft 6in x 2ft x 1ft 9in, [75 x 60 x 55 cm] with two 1.5in [4 cm] diameter hazel poles fixed under the border across the length of the hamper about 6in apart and 6in [15 cm] from the side border. Dead rabbits were tied together by their hind legs and hung over the poles so that their heads hung down just above the bottom of the hamper. Doreen remembers in the days when greengrocers used to sell their wares from horse drawn carts in the streets and seeing rabbits being offered for sale carried in wicker hampers.
Boiling of the willow was carried out in the yard next to the workshop in a large tank which had to be filled each time with fresh water from an adjacent hand operated pump. I and, before me, your Dad were frequently the motive power for the pump."
I cannot add much to this except that cycle baskets, mainly made for the Co-operative Society to very exacting measurements, were very much part of the business at the turn of the century, and that in 1922 the men produced about 30 rabbit hampers per week for which they received 1/9 each. [The purchasing power of 1/9 is equivalent to about £3.30 today.]
The baskets were not only sold in Birmingham Market, for many firms from Smithfield bought rabbit hampers in baffling numbers: in January 1929 one hundred and forty-seven hampers were sold. Considering how little representation rabbit meat has in the modern diet these numbers are very surprising.
Depending on how many were bought, the hampers were sold from 3/8 to 4/- . A basket would be sold for at least twice these prices and more than a pound for the larger laundry baskets.
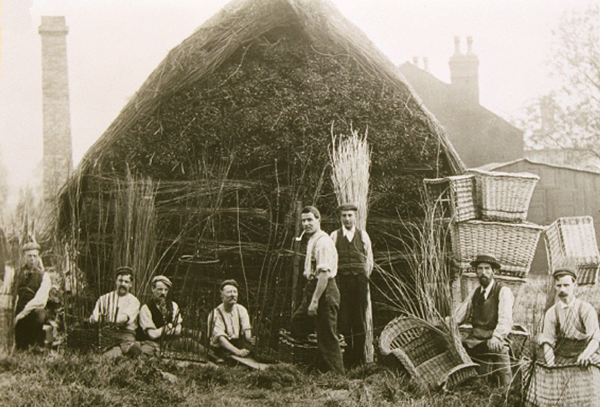 |
‘Charl’ (third from right) in front of the rick of withies, with his father, James (second from right) in Birch Road in about 1905. |
On the death of James Charles Turner in 1981 the traditional craft of the willow, the craft followed for at least five generations, died with him.
Peter C Turner, BA, Halesowen
References and notes
1 |
|
Rosser, A.N. 1999 "The Quinton and Round About", Vol 1, 1998 & Vol. 2, 1999, Quinton History Society |
2 |
|
Brit. Amalg. Union of Journeymen Basket, Cane and Wicker Furniture Makers, 1916, List of Prices etc., Derby |
3 |
|
Turner, J. Personal Communication |
4 |
|
In the photograph at the end of this article: James and Arthur on the right are working on the more demanding articles |
5 |
|
White willow was produced by stripping the bark off the osier while the sap was still in the stems. |
This
article © Peter C Turner 2009 - contact
for permission to reproduce |